

Regarding its production, in 2017 they recorded 9.2 million units in manufacturing, while there was an increase in 2018 of a total of 9.7 pieces. In the last years, due to the work demand, Bosch Aguascalientes has increased the plant surface, reaching the 13,000 square meters in production areas, engineering, and offices, with a total of 38,000 square meters. “These brakes are 100 % programmable, the pedal can be changed, its sensation, more aggressive, sporty or soft, depending on the vehicle, we are already manufacturing since last year, it is used in futurist cars as well as in Tesla to a CR-V Honda, every time it is permeating more,” added Orlando Ramirez, plant manager at Bosch Aguascalientes.
#Brake pedal for bosch ibooster software
The iBooster is a brake thought for new vehicles such as the Tesla, Audi or BMW, since it is completely electronic mechanic, although it has engines it is 100 % controlled by an Electronic Control Unit or Engine Control Unit (ECU,) better known as automotive computer, this way it can receive software online updates from the vehicle, in case there is an improvement, there is a ‘patch’ that sends it to the brake, therefore, it is updated and the problem corrected. The German plant is the first one to manufacture automated brakes iBooster Generacion 2, same that started to be industrialized in 2018 They also manufacture anti-block braking system (ABS G9) and electronic stability program (ESP,) same that were created by Bosch since the 70s, these products have achieved their main objective which is saving countless lives in highways. Fortunately, the second time was the charm and K-Motor Performance had the solution.Given the demand for their products and the proximity with their customers, in 2004, Bosch began operations in Aguascalientes. No one seems to spec how far the threads extend which required looking at a lot of pictures to find one that would work. D’oh! The seat is deeply recessed and the hex nut bottomed before the flare seated. The master cylinder has two M12 x 1.0 mm pressure ports, so I purchased a set. For this, a complex brake system is necessary, in this case consisting off a Bosch iBooster. However, I think that the single input rod drives two internal master cylinders (the reservoir has two feeds) and I have no idea how that changes things. and the mechanical brake when the brake pedal is pushed. But I can’t determine how it’s actually adjusted. From what I can tell, the master cylinder has a 1” bore which would mean that I shouldn’t need much travel. The iBooster is a vacuum-independent and electromechanical brake booster. This resulted in about 5-1/4” pedal travel, as measured from the middle of the pedal, and about 15/16” of master cylinder travel. Without any fluid in the system, I pressed the brake pedal until it bound on the adapter bar.
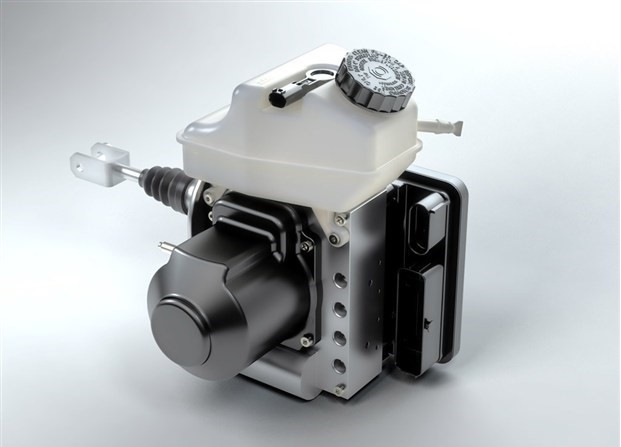

I’m worried about having enough master cylinder travel so the iBooster is spaced 1/4” off of the bracket, the tubes were left long and the tube ends are only lightly tacked. While the base of the tubes were jigged, I didn’t jig the ends of tubes and one of them warped inwards during welding, so I’ll need to remake this part. It would have been less work to fillet weld the tubes to the bar, but the bored holes help jig the tubes during welding and they result in a stronger assembly. The center was tapped for the input shaft’s M10 x 1.5 mm thread and I bored holes 80% of the way into bar to receive the tubes. The iBooster provides the same interfaces to the brake pedal, bulkhead and the ESP® system as today‘s vacuum brake boosters. Note that some OEMs utilize an extension rather than a clevis. I removed the clevis from the iBooster’s input rod to keep everything compact and to reduce the number of connections that might introduce play into the braking motion. The 5/16"-24 rod ends are held in place by grade 8 washers and hex bolts with drilled heads so that they can be safety wired. While there should be minimal lateral forces, I laser cut retention discs from 0.060" stainless steel to restrict lateral movement. Using the lathe, I machined the rod a few thousands wider than the pedal and drilled and tapped 5/16"-24 holes in the ends.
